General Information
Chemical & Physical Properties
Safety Information
Synthetic Route
Common Names |
Polyacrylic acid|Propenoic acid polymer|Acrylic acid polymer |
Structure |
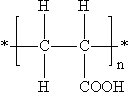 |
CAS No. |
9003-01-4 |
Boiling Point (℃) |
116ºC |
Molecular Weight |
2000(Average) |
Melting Point (℃) |
106ºC |
Appearance |
Colorless viscous liquid |
Vapor Specific Gravity |
N/A |
HS Code |
3906909090 |
Flash Point (℃) |
61.6ºC |
Solubility |
Soluble in water. |
Autoignition Temperature (℃) |
N/A |
Safety Phrases |
S24/25 |
RIDADR |
UN 3265 8/PG 3 |
WGK Germany |
3 |
Packaging Group |
N/A |
Hazard Class |
N/A |
|
SYMPTOMS |
PREVENTION |
FIRST AID |
Inhalation |
Cough. Sore throat. |
Use local exhaust or breathing protection. |
Fresh air, rest. |
Skin |
Redness. Burning sensation. Itching. |
Protective gloves. |
Remove contaminated clothes. Rinse and then wash skin with water and soap. |
Eyes |
Redness. Pain. |
Wear safety goggles. |
First rinse with plenty of water for several minutes (remove contact lenses if easily
possible), then refer for medical attention. |
Ingestion |
Abdominal pain. Nausea. Vomiting. |
Do not eat, drink, or smoke during work. Wash hands before eating. |
Rinse mouth. Induce vomiting (ONLY IN CONSCIOUS PERSONS!). Refer for medical attention. |
It is obtained by polymerization of acrylic acid as a monomer in the presence of an initiator.
Preparation method of acrylic acid
a. Cyanethanol method using chloroethanol as raw material, and sodium cyanide guade cyanide cyanide
cyanide ethanol. Cyanoethanol is hydrolyzed at 175 °C to obtain acrylic acid in the presence of sulfuric
acid.
b. Acrylonitrile hydrolysis method Using acrylonitrile as raw material in the presence of sulfuric acid
hydrolysis to generate sulfate of acrylamide, and then hydrolysis to obtain acrylic acid.
c. Repe method and modified Repe method Acetylene was dissolved in tetrahydrofuran and added to the
reactor after measurement. In the presence of a catalyst composed of nickel bromide and copper bromide,
carbon monoxide and water are passed, and 7.8~9.8 MPa is reacted at 200~225 °C.
d. Acrolein oxidation method The propylene, air and water are mixed in a ratio of 1..10..6 (V), and then
passed into the first boiling bed, and under the catalysis of aluminum, vanadium, phosphorus, iron,
aluminum, nickel and potassium, it stays at 370~390 °C for 5.5s, and the linear speed is 0.6m/s. Then
enter the second boiling bed, under the catalysis of aluminum-vanadium = tungsten, stay for 2.25s, and
the reaction temperature is controlled at 270~300 °C. The empty time yield of acrylic acid is 55~60
kg/m·h, which is safe, light pollution and low cost, and is the main method of domestic and foreign
production.
Preparation of polyacrylic acid Add deionized water to the polymerization kettle, heat 60~100 °C, and
start dropping the mixed solution of ammonium persulfate and acrylic acid (configured with deionized
water). After dripping, continue to keep warm and stir for 3~4h. Ready-to-be-the-fly product. Add 530kg
of deionized water to the polymerization kettle, add 41kg of flat and add OS-15 to stir and dissolve.
Then add 4kg of sodium dodecyl sulfate, stir and dissolve and add 68kg of mixed monomer (butyl acrylate,
acrylonitrile) within 20min. After stirring for 15m, add 30kg of 1.5% ammonium persulfate aqueous
solution, and add it within 30min. Continue stirring for 15min, slowly raise the temperature to 70 °C,
and start adding the mixed monomer (272kg) dropwise, about 1h drop. After addition, keep warm and stir
at 80 °C for 1h.
After the reaction, cool down to about 40 °C, add 70kg flat plus OS-15, stir for 15min and filter to
remove impurities to obtain the product
e. Using solution polymerization method, using acrylic acid as raw material, diluted with water,
polymerization under the action of initiator. Acrylic polymerization is fast and exothermic, in order to
achieve the control of the polymerization process, polyacrylic acid for circulating water treatment in
the preparation, usually acrylic acid is formulated into an aqueous solution below 40% for
polymerization, the polymerization temperature is usually controlled at 50~150 °C. Commonly used
initiators are ammonium persulfate and sodium sulfite, which are often used in the polymerization
process
Add a small amount (< 5%) mercaptosuccinic acid, isopropanol, etc. as a retarding agent, and
hydroquinone or catechol as a polymerization inhibitor. A certain amount of stodoxically deionized
water is added to the reactor equipped with an electric stirrer, a reflux condenser, a drip funnel
and a thermometer, stirring is started and the reaction temperature is raised to about 80 °C, and
the metered thioglycolic acid or isopropanol is added to the reactor and miscible with water. The
stoichiometric ammonium persulfate is prepared into a dilute solution with metered water, placed in
a drop funnel on the polymerization reactor, and the metered acrylic acid (AA) monomer is mixed with
a certain amount of water and placed in another drop funnel on the polymerization reactor. When the
water temperature in the reactor reaches the temperature required for the reaction, the aqueous
solution of acrylic monomer and the aqueous solution of the initiator ammonium persulfate are added
dropwise, and the drop acceleration is controlled to make the reaction temperature between 85~90 °C,
and the polymerization reaction is 3~5H. After the completion of the reaction, the polymer liquid is
cooled to room temperature, and various technical indicators are sampled and analyzed, and the
requirements are dispensed.